Rivian’s R2: Cost-cutting Measures & Production Boost
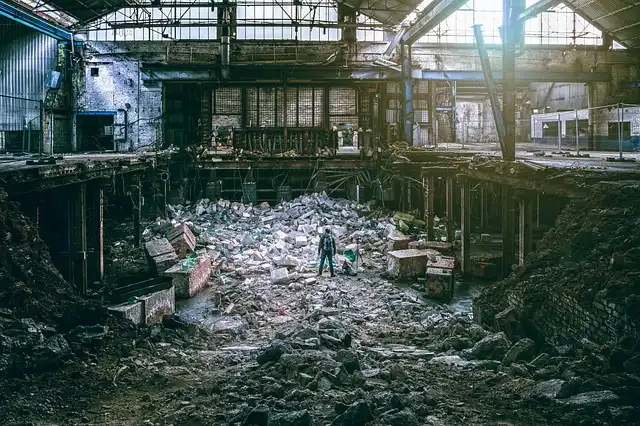
Earnings. It’s what makes or damages automobile start-ups, and Rivian is no stranger to this principle. The manufacturer of the excellent R1S and R1T EVs turned a gross profit for the second quarter straight at the beginning of this year, but that’s not nearly enough.
The short solution is: through smart remedies that minimize manufacturing prices while optimizing profit margins. Possibly the very best visuals representation of exactly how Rivian intends to achieve this is embedded listed below. The picture was posted on X by the start-up’s creator and CEO, RJ Scaringe, and it shows the difference between the body circuitry harness of the upcoming R2 and the existing, updated R1 models.
R2 Wiring Harness Innovation
According to Scaringe, the R2 will certainly have just 3 spreadings in the back, whereas the R1 has about 50 stampings and over 300 joints. This makes production and assembly much simpler, yet it may confirm bothersome when crash repairs will certainly need to be performed.
That’s not all. In other social media sites blog posts, Scaringe boasted exactly how the R2’s electric motor inverter uses 41% less parts than the Enduro drive device that’s used on the R1S and R1T. Creative remedies like integrating the drive system install right into the inverter lid, in addition to using the inverter framework to close out the oil cooling path, additionally contribute to the overall expense financial savings effort.
Electric Motor Efficiency
Here’s where the upcoming R2 SUV enters into play. It’s slated to take place sale in the Untied States the initial fifty percent of next year with a beginning rate of around $45,000, positioning it in the highly affordable electric mid-size crossover section that’s presently ruled by the Tesla Model Y.
According to Rivian, the R2’s harness is 44 pounds (20 kilos) lighter and utilizes 2.3 miles less wires, along with 60% less in-line adapters. The front section harness is a significant separation from what’s currently being utilized, and it deserves stating that the California-based EV manufacturer currently overhauled the R1’s wiring harness by cutting 1.6 miles for the rejuvenated variation.
When it comes to the body of the R2, Rivian will make use of large high-pressure die spreadings for the SUV’s framework, which resembles what Tesla has been utilizing for several years through its megacasting technology.
Large Scale Production
That’s suitable for a startup. To play in the big league, nevertheless, Rivian demands to sell many more cars, and the R2 is anticipated to do simply that. The company’s existing factory in Normal, Illinois, is being updated to be capable of putting together as much as 155,000 vehicles per year, while Rivian’s new factory in Georgia will have an outcome of 400,000 vehicles per year when completely functional.
In other social media posts, Scaringe boasted just how the R2’s electrical motor inverter uses 41% less components than the Enduro drive unit that’s made use of on the R1S and R1T. To play in the big organization, however, Rivian needs to sell many even more cars and trucks, and the R2 is expected to do simply that. The business’s present factory in Typical, Illinois, is being updated to be capable of constructing up to 155,000 automobiles per year, while Rivian’s new factory in Georgia will certainly have an output of 400,000 lorries per year when completely functional.
1 Cost Reduction2 electric vehicles back
3 EV Production
4 Manufacturing Efficiency
5 Rivian R2
6 RJ Scaringe
« BMW: EV Challenges & Market Shifts in Auto IndustryHyundai’s AI EV Charging Robot: A Tesla Alternative »